变形金属超声检验方法
Ultrasonic inspection of wrought metal
2004-09-01 发布 2004-12-01 实施
国防科学技术工业委员会 发 布
GJB 1580A-2004
代替 GJB 1580-1993 和 GJB 593.1-1988 FL 0140
GJB 1580A-2004
I 目 次
前言……………………………………………………………………………………………………………II
1 范围…………………………………………………………………………………………………………1
2 规范性引用文件……………………………………………………………………………………………1
3 一般要求……………………………………………………………………………………………………1
3.1 检验人员…………………………………………………………………………………………………1
3.2 环境条件…………………………………………………………………………………………………1
3.3 设备………………………………………………………………………………………………………1
3.4 试块………………………………………………………………………………………………………3
3.5 耦合剂……………………………………………………………………………………………………5
3.6 受检件……………………………………………………………………………………………………5
3.7 检验规程(或检验图表)…………………………………………………………………………………5
3.8 扫查的进行………………………………………………………………………………………………6
3.9 检验记录…………………………………………………………………………………………………6
3.10 检验结果的处理…………………………………………………………………………………………7
3.11 受检件标记………………………………………………………………………………………………7
3.12 受检件的腐蚀防护………………………………………………………………………………………7
3.13 检验报告…………………………………………………………………………………………………7
4 纵波检验……………………………………………………………………………………………………7
4.1 检验范围…………………………………………………………………………………………………7
4.2 检验………………………………………………………………………………………………………8
5 横波检验……………………………………………………………………………………………………11
5.1 适用性……………………………………………………………………………………………………11
5.2 检验………………………………………………………………………………………………………11
5.3 评定………………………………………………………………………………………………………13
附录 A (规范性附录) 超声检验仪与探头配用时的使用性能测试方法………………………………14
附录 B (资料性附录) 人工反射体的硅橡胶覆型检查方法……………………………………………19
附录 C (规范性附录) 纵波检验用标准试块……………………………………………………………20
附录 D (规范性附录) 曲面纵波检验用标准试块………………………………………………………22
附录 E (规范性附录) 横波检验用平表面试块…………………………………………………………24
附录 F (规范性附录) 实心圆柱体对比试块……………………………………………………………26
附录 G (规范性附录) 圆筒形对比试块…………………………………………………………………27
GJB 1580A-2004
前 言
本标准代替 GJB 1580-1993《变形金属超声波检验方法》和 GJB 593.1-1988《无损检测质量控制
规范 超声纵波和横波检验》。
本标准与 GJB 1580-1993 及 GJB 593.1-1988 相比,主要差别如下:
a) 对两份标准中不一致的内容进行了统一,如工作频率、标准试块的检定周期、受检件表面粗糙
度和扫查间距等;
b) 对平底孔加工要求、探头频率的检验要求、液浸槽尺寸的要求等内容进行了修改;
c) 增加了平底孔质量检验方法、专用试块的制作要求、液浸法检验声束入射角的调整方法和要求
等内容。
本标准的附录 A、附录 C、附录 D、附录 E、附录 F、附录 H、附录 G 为规范性附录,附录 B 为资
料性附录。
本标准由中国航空工业第一集团公司提出。
本标准由中国航空综合技术研究所、北京航空材料研究院归口。
本标准起草单位:中国航空工业第一集团公司北京航空材料研究院、航天 703 所、航空 430 厂。
本标准主要起草人:梁 菁、史亦韦、何双起、李 泽。
GJB 1580-1993《变形金属超声波检验方法》于 1993 年 3 月首次发布,GJB 593.1-1988《无损检
测质量控制规范 超声纵波和横波检验》于 1988 年 8 月首次发布。
II
GJB 1580A-2004
1
变形金属超声检验方法
1 范围
本标准规定了用超声(纵波或横波)脉冲反射(液浸或接触)检测技术检验变形金属及其制件的一般
要求和纵波检验及横波检验要求。
本标准适用于锻坯、锻件、轧制件、板材、挤压或轧制棒材、型材,以及由其经机加工制成零件的
超声检验。
2 规范性引用文件
下列文件中的条款通过本标准的引用而成为本标准的条款。凡是注日期的引用文件,其随后所有的
修改单(不包含勘误的内容)或修订版均不适用于本标准,然而,鼓励根据本标准达成协议的各方研究是
否可使用这些文件的最新版本。凡是不注日期的引用文件,其最新版本适用于本标准。
GB/T 12604.1 无损检测术语 超声检测
GB/T 18694 无损检测 超声检验 探头及其声场的表征
GB/T 18852 无损检测 超声检验 测量接触探头声束特性的参考试块和方法
GJB 9712 无损检测人员的资格鉴定与认证
JB/T 10063-1999 超声探伤用 1 号标准试块 技术条件
3 一般要求
3.1 检验人员
从事超声检验工作的人员应按 GJB 9712 取得技术资格证书。各级人员只能从事与其技术资格等级
相应的工作。
3.2 环境条件
3.2.1 场地
超声检验不应在影响正常工作的强磁、震动、高频、灰尘大、有腐蚀性气体及噪音大的场地进行。
工作场地应避开明亮的光线。
3.2.2 温度及湿度
工作场地的温度及湿度应控制在仪器、设备及材料所允许的范围内。
3.3 设备
3.3.1 超声检验仪
脉冲发生器和接收器的频率特性应与所用探头相匹配。超声检验仪在经过修理后投入使用前,或每
年应至少校验一次使用性能,以确认其仍满足要求。校验时采用的测试方法见附录 A,使用性能的最低
要求见表 1。表 1 中的最低要求数据均为仪器与换能器直径不大于 14mm 的 5MHz 探头匹配时的要求。
每次校验的数据均应保存备查。针对每一检测对象,仪器与探头配用的灵敏度、分辨力和信噪比应满足
检验要求。
3.3.2 电源
在信号幅度调整到显示屏满刻度 50%的情况下,电源电压波动引起的信号幅度变化不应超过满刻
度的±2.5%,否则应使用稳压器或更换电池。
GJB 1580A-2004
2
表 1 仪器使用性能的最低要求
仪器使用性能 最低要求
垂直极限 满刻度
垂直线性上限 满刻度的 95%
垂直线性下限 满刻度的 10%
水平极限 满刻度
水平线性范围 不小于满刻度的 85%
灵敏度 100%a
信噪比 100%/20%a
入射面分辨力 优于 10mmb
衰减器 见附录 A 中表 A.1
a
铝合金材料中埋深不小于 75mm 的直径 0.4mm 平底孔反射波高至少达到满刻度的 100%,同时噪声水平不大
于 20%,则视为灵敏度和信噪比满足要求。
b
入射面分辨力在铝合金标准试块中直径 1.2mm 平底孔上测定。
3.3.3 探头
3.3.3.1 概述
探头在投入使用前均应编号,并测量其回波频率、距离-幅度特性及声束特性(楔块有弧度的圆弧
探头测试方法和要求,根据具体情况由使用单位自行确定)。测试方法推荐采用 GB/T 18694 和 GB/T
18852,所有的测试记录均应保存备查。
对于频率在 2.25MHz~10MHz 范围内的探头,其回波频率与标称值的偏差应在标称值的±10%以
内。
在用的纵波探头的距离-幅度特性至少每六个月检查一次,斜探头及双晶纵波探头至少每三个月检
查一次,并与原始曲线比较,幅度最大偏差超过 20%的探头不应使用。
3.3.3.2 纵波直探头
纵波探头的换能器直径一般应在 6mm~25mm 之间。在评定所发现的不连续性尺寸时,应采用换
能器直径不大于 20mm 的平圆探头。
纵波探头的声束特性要求在最后一个声压极大值(Y0+)处,沿相隔 45˚的四个方向测量时,不应有明
显的副瓣,最小波束直径与最大波束直径(6dB 点)之比不应小于 0.75,如图 1 所示。
Y0+
—最后一个声压极大值;Y1-—最后一个声压极小值
图 1 探头距离-幅度曲线
距 离,mm
Y0+ Y0-
反射波高,dB
GJB 1580A-2004
3
3.3.3.3 斜探头
用于接触法检验的斜探头,应测量入射点和钢中折射角,测量的频次应根据扫查的工作量及工作条
件来确定。当斜楔经修理或更换以及在测定不连续性的位置时也应检查入射点和折射角。钢中折射角与
标称值相差 2˚以上的探头应修正,否则不允许使用。
3.3.4 液浸槽及探头操纵装置
用于液浸法检验的液槽尺寸应合理,应能浸没所检部位并保证探头在所需的工作范围内运动,同时
也应方便操作。
探头操纵装置应能在两个相互垂直的平面内以不超过±0.5˚的误差提供探头角度调节。桥架应有足
够的强度以便对操纵装置提供刚性的支持,并能平滑准确地将探头定位于所需的位置上。机械装置在按
设定的距离扫查时,距离偏差应不超过±2.5mm/m。扫查间距应满足实际检验的需要。
转动夹具应能夹住受检件,使其在所要求的扫查速度下作顺时针或逆时针方向的平稳转动。转动夹
具应有中心定位装置,使受检件和转动夹具同心,偏差不应超过 0.5mm。
3.4 试块
3.4.1 人工反射体
根据检验要求,试块中的人工反射体可以选用平底孔、横孔或切槽。其中平底孔是超声纵波检验最
基本的反射体。反射体的尺寸可采用常规物理测量方法进行检验,或用硅橡胶覆型法进行检验,硅橡胶
覆型法参见附录 B。
3.4.2 标准试块
用于纵波检验的铝合金标准试块,其材质、尺寸及加工要求等应符合附录 C 的要求。用于纵波和
横波检验的钢制 1 号标准试块,其材质、尺寸及加工要求等应符合 JB/T 10063-1999 的要求。
标准试块每五年应送检定机构检定一次,但使用单位应定期检查试块外观有无影响使用的表面损
伤。
3.4.3 对比试块
3.4.3.1 概述
3.4.3.1.1 对比试块材料与受检件的透声性、声速和声阻抗应是相似的。若尺寸、材料等的要求与标
准试块相同,则标准试块也可用作对比试块。一般情况下,检查铝合金、镁合金、钛合金及低合金钢时
对比试块的用料可按表 2 选定。但不锈钢、镍基合金、钴基合金检验用对比试块应采用被检件材料来制
作,钛挤压件检验用试块应采用与受检件相同的挤压材料来制作。
表 2 对比试块的制作用料
受检件材料 对比试块用料
铝合金 7A09 或 2A12,淬火、人工时效
镁合金 MB15
钛合金 TC4,退火
低合金钢、低合金高强度钢、碳钢及工具钢 40CrNiMoA,退火
3.4.3.1.2 利用垂直入射超声纵波,在检验要求规定的工作频率下进行对比试块材料检验时,不应有
任何高于噪声信号幅度的回波显示,且任何部位由材料引起的底反射幅度变化均不应大于 3dB。
3.4.3.1.3 对于每套试块(不少于 12 块)材料,在制作前应采用液浸法测定其透声特性的一致性。对每
一厚度的试块材料测量将一次底面反射信号幅度提高到前表面反射信号幅度所需的增益量,将结果画成
分贝值与材料厚度的关系图,通过各数据点画出最佳拟合线。对于可接受的一套试块料,不应有任何点
与此拟合线相差大于±1dB(参见图 2)。
3.4.3.1.4 对比试块在投入使用前,应按图样要求进行检验。检验合格后应进行孔的封堵。使用单位
GJB 1580A-2004
4
应定期检查试块外观有无影响使用的表面损伤。
图 2 可用的一套试块用料的声衰减特性
3.4.3.2 纵波检验用试块
3.4.3.2.1 平表面试块
平表面试块的形状和尺寸要求见附录 C。
对于成套试块,在制作后应采用液浸法测定其距离―幅度曲线,即测出将每一平底孔回波提高到相
同幅度时所需分贝增益值与金属声程的关系,通过数据点画一最佳拟合线。对于一套可接受的试块,不
应有任何点与拟合线相差超过±1dB。如图 3 所示。
图 3 可接受的一套试块的距离-幅度曲线示例
3.4.3.2.2 曲面试块
曲面试块是在检验曲面时采用的对比试块。曲面试块的形状和尺寸要求见附录 D。实心圆柱体应尽
量使用与被检件直径相同的棒材制作。通常曲率半径为 125mm 或更大的曲面可使用平面试块。
最佳拟合线
平底孔埋深,mm
048
12
16
20
24
28
32
36
25 50 75 100
最佳拟合线
材料厚度,mm
0
4
8
12
16
20
24
28
32
25 50 75 100
2dB
相对幅度,dB
2dB
相对幅度,dB
GJB 1580A-2004
5
3.4.3.3 横波检验用试块
3.4.3.3.1 平表面试块
用横波检验平表面受检件或异型件的平坦部位时,可采用附录 E 所示的试块。
3.4.3.3.2 实心圆柱体试块
用于圆柱体受检件周向检验的试块,可按附录 F 中的要求制作。
3.4.3.3.3 圆筒形试块
检验壁厚为 3mm~25mm 圆筒形受检件时,所用试块可按附录 G 中的 G.1 要求制作。
检验壁厚不大于 3mm 的圆筒形受检件时,可在受检件半径上加工尺寸符合要求的切槽作为反射体,
槽尺寸由供需双方商定。所用试块可按附录 G 中的 G.2 要求制作。也可在圆筒内外壁上用电火花方法
加工的“U”槽的侧面作为反射体,其长度、深度和宽度应符合相应技术文件的要求。
3.4.3.4 专用试块
在受检件的几何形状决定了需要用实际零件或零件复制件制作对比试块时,所有人工反射体都应按
纵波或横波检验的具体要求制作。
3.4.4 试块标记
试块均应作出标记,以便识别出材料牌号、孔或槽的尺寸、孔的角度和(或)深度等。
3.5 耦合剂
3.5.1 液浸法
可采用清洁水作为耦合剂,水中应无气泡及其它妨碍超声检验的外来物。必要时,可在水中加入适
量的防蚀剂,但应确认添加的物质不会对受检件及设备造成损害。
3.5.2 接触法
所用的耦合剂不应有损于探头和受检件。常用的耦合剂有水、油类、脂类、水溶性凝胶等。耦合剂
的粘度及表面润湿性应根据受检件的表面粗糙度来选择,应保证声的能量能很好地传入受检件。
3.6 受检件
3.6.1 外形
受检件一般应在精加工前完成检验。对于不能一次完成所有部位检验的复杂外形锻件,应在原材料、
锻件毛坯、机加工各阶段对可能检验的部位分别进行检验。
3.6.2 表面状态
受检件表面不允许存在影响超声检验的松动的氧化皮、折叠、毛刺、油污等。若个别部位不可能清
除,应在受检件上作出标记,供评定时参考。
受检件表面粗糙度,对于 AAA 级检验 Ra 值应不大于 1.6µm;对于 AA 级和 A 级检验 Ra 值应不大
于 3.2µm;对于 B 级检验 Ra 值应不大于 6.3µm。表面车削应采用圆头刀具。由于表面粗糙度本身并不
能反映所有的表面特征,因此有时可能需要进一步改善表面状态或提出更高的表面粗糙度要求。
3.6.3 材料状态
一般情况下,受检件应在供货的热处理状态下进行检验,最终检验应尽可能在制件最终热处理之后
进行。对于变形铝合金,应在最终热处理之后进行检验,若在其它阶段进行,应由供需双方商定。
进行超声检验的材料,其噪声显示信号幅度应比要求检出的最小不连续性显示信号幅度至少低
6dB。
3.7 检验规程(或检验图表)
3.7.1 概述
检验规程应在对受检件的情况进行充分了解的基础上编写。需要了解的内容包括材料牌号、热处理
状态、制造方法、加工余量、影响其使用的不连续性种类和最大可能取向、受检部位受力方向及验收要
求等。检验规程的内容一般应包括:
a) 检验单位的名称;
GJB 1580A-2004
6
b) 规程的编号、编制和修改的日期、编制规程依据的文件号;
c) 受检件的名称、图号、检验工序号、材料牌号及热处理状态;
d) 采用的检测技术;
e) 受检件的草图,图上应标明检验部位、超声入射面及其粗糙度,由于某种原因(如盲区、形状
等)不连续性不能被发现的区域,各部位的验收等级;
f) 超声检测仪及配用设备的型号;
g) 探头型号及探头的其它重要参数;
h) 耦合剂的名称及牌号;
i) 检验仪和探头操纵装置的调整,包括所用对比试块的编号;
j) 探头相对于受检件表面的位置、扫查方式、扫查速度及扫查间距;
k) 不连续性的评定方法及验收要求;
l) 标记的部位及方法;
m) 其它需要说明的情况。
3.7.2 声束入射方向和入射面的选择
入射方向的选择应使声束中心线与不连续性反射面,特别是与最大受力方向垂直的不连续性反射面
尽可能垂直。上述不连续性反射面的最大可能取向应根据成型工艺和组织的情况来确定。一般情况下:
a) 锻件、挤压件、棒材和板材声束应垂直于流线方向;
b) 横截面长边和短边长度比小于 3׃1 的矩形截面体应沿横截面的长边和短边方向进行检验;
c) 正方形自由锻件至少在三个相邻的面进行检验。
3.7.3 检验频率的选择
对于给定的受检件,超声检验频率应根据要求发现的不连续性的性质、尺寸以及受检件的材质等情
况来选择。
注:一般情况下,较高的频率可提高声束指向性、提供较好的纵向和横向分辨力;较低的频率可提供较好的穿透能
力和提高探测取向不甚有利的平面型不连续性的能力。
3.7.4 扫查速度的选择
采用的扫查速度,应保证在所要求检测的金属声程处,规定等级的最小尺寸不连续性能得到可重复
的显示,在自动记录时能可靠地启动调定的报警或记录装置。在一般情况下,目视监测时的扫查速度不
宜超过 50mm/s。
3.8 扫查的进行
扫查应按照检验规程进行。
在每次检验开始前和结束后、在仪器的调整或插接件有任何改变时,均应检查仪器及探头操纵装置
的调整情况。当连续工作时,建议根据具体情况和要求,增加仪器设备的检查频度。如发现调整得不正
确或发现设备有问题,则在发现有问题之前和上次调整之后所检验过的全部受检件应重新检验。检验大
型件时,在检验每一件的前后均应检查调整情况。
在检查形状规则及上下面平行的受检件,如板、棒、挤压件时,可将报警或自动记录与目视监测超
声仪显示屏结合使用。
3.9 检验记录
检验记录的内容一般应包括:
a) 送检单位及送检日期;
b) 受检件名称、图号、零件号、炉批号、工序号及数量;
c) 所采用的检验规程编号;
d) 所用的仪器、探头、试块、耦合剂;
e) 检测灵敏度的调整情况,包括声传输修正情况;
GJB 1580A-2004
7
f) 任何反射波高超过所规定验收要求的不连续性的平面位置、埋藏深度、波高超出的分贝数以及
其它认为有必要记录的内容;
g) 检验人员及检验日期。
检验记录应编号保存,保存期限按有关单位的规定。
3.10 检验结果的处理
所含不连续性超过规定要求的受检件应属不符合要求件。但对于需机加工的零件,当不连续性指示
超过规定要求时,只要在以后的加工中可以除去,则是允许的。对于这样的受检件应做详细核查,对不
连续性准确定位,以确认可被加工掉。详细情况应在检验记录和报告中说明。
3.11 受检件标记
3.11.1 所有受检件均应作出明显标记。对于符合验收要求的受检件,标记的方法和部位应不影响受检
件的使用,且在后续加工中不被去除。如后续加工中可能会去除所做标记,或在锭、节号齐全的情况下,
可在书面报告中用文字或符号说明。
3.11.2 根据具体情况,经允许可采用钢印、腐蚀等标记方法。对于因表面粗糙度或功能要求不宜采用
钢印、腐蚀方法时,可采用其它的替代方法,如涂色法或标签法。
3.12 受检件的腐蚀防护
检验完成后应及时清除受检件上的耦合剂。对于液浸法,受检件在槽中的时间不应超过检验所需的
时间。在完成检验后,受检件应从槽中取出并使其干燥。所有精加工件,在干燥后均应涂上防腐剂。
3.13 检验报告
检验报告一般应包括以下内容:
a) 报告编号;
b) 送检单位;
c) 受检件名称、图号及编号、材料牌号;
d) 检验规程的编号;
e) 验收要求;
f) 不符合验收要求的不连续性的位置、当量尺寸及分布示意图;
g) 评定结论;
h) 检验人员、审核人员、专业负责人及日期等。
检验报告应至少一式两份,由检验单位和送检单位各持一份,检验报告应作为质量档案保存。
4 纵波检验
4.1 检验范围
4.1.1 检验至少应包括使声束垂直入射到与主流线平行面的扫查。
4.1.2 当入射面分辨力不足以分辨靠近声入射面的不连续性时,应从对面进行附加的扫查或制定另外
的分区要求。必要时可由供需双方商定另外的附加扫查(如使用横波),或增大加工余量。
在未给定声入射面加工余量的情况下,入射面分辨力的要求见表 3,但对于铝合金锻件,入射面分
辨力的要求见图 4。 表 3 入射面分辨力要求
入射面分辨力要求
mm 受检件厚度 h
mm
锻件(铝合金锻件除外) 其它材料
<32 ≤6.4 ≤3.2
≥32~64 ≤6.4 ≤0.1 h
≥64 0.1 h 或 12.5,取小值
GJB 1580A-2004
8
图 4 铝合金锻件入射面分辨力要求
4.1.3 对于每一检查方向,若最大有效金属声程使得仅从一面检验无法探出所规定验收等级的最小不
连续性,则应从对面进行再次检验。
4.2 检验
4.2.1 仪器灵敏度的调整
可用两块带平底孔的试块来调整仪器灵敏度,第一块中平底孔孔底与声入射面的距离(埋藏深度)
应不大于受检件入射面的加工余量;第二块的高度应与受检部位材料厚度相同,而在其底面所钻平底孔
的深度应不大于受检件底面的加工余量,在可以确认底面分辨力满足要求的情况下,也允许采用与第二
块试块规定的平底孔埋深相同或稍大,但孔深大于受检件底面加工余量的试块。平底孔直径由所规定验
收等级决定。一般情况下,应使来自任一试块中平底孔的反射波高至少为显示屏满刻度的 80%。除非
另有规定,超声检验仪的“抑制”应处于关闭位置。
4.2.2 传输修正
4.2.2.1 在对比试块与受检件之间存在有声传输特性的差异时,应考虑进行声传输修正。修正值一般
可通过比较试块的底面反射幅度值与受检件等厚度部位的底面反射幅度值的分贝差来确定。
4.2.2.2 若对比试块与受检件之间传输修正值超过±6dB,则该对比试块不应采用。
4.2.2.3 若对比试块与受检件之间传输修正值在±2dB 以内,可不进行修正,但应得到需方的同意。
4.2.3 液浸法检验时液程和声束入射角度的调整
4.2.3.1 液程的调整
可用 4.2.1 的两试块来确定液程,应以达到最佳分辨力和最佳穿透力的组合为原则,且应使受检件
的二次前表面反射出现在一次底面反射之后。
调节灵敏度、扫查受检件及评定不连续性时,所用液程相差不应超过±3mm。
4.2.3.2 声束入射角度的调整
在纵波直入射检验时,一般通过调节声束入射角,使入射面的反射信号幅度最高,此时可认为声束
垂直于入射面。在采用聚焦探头时可采用多次反射法来进行入射角度的调整。在检验中,已确定的角度
的变化不应超过±0.5˚。当检查曲面零件时,可采用曲面跟踪装置,以保证声束的垂直入射。
纵波斜入射检验时,在将声束入射角调整到垂直入射状态后,按要求的角度偏转,一旦角度确定,
角度的变化不应超过±0.5˚。
4.2.4 扫查间距的确定
4.2.4.1 对于圆换能器探头,分别在 4.2.1 所用试块的每一块上调整仪器灵敏度,使孔底最大反射波高
为显示屏满刻度的 80%,然后找出探头沿孔径方向移动时反射波高下降 6dB 的两点间距离,即为有效
声束宽度。扫查间距不应大于其中较小有效声束宽度的二分之一。
4.2.4.2 对于双换能器纵波探头,可在 4.2.1 所用对比试块中埋深较小的一块上调整仪器灵敏度,使来
自孔底的最大反射波高为显示屏满刻度的 80%,沿与隔声层取向平行的方向横过平底孔直径移动探头,
以找出反射波高下降 6dB 的两点间距离。同样在埋深较大的一块上进行测量,可得到另一下降 6dB 的
从入射面算起的最大尺寸,mm
18
15
12
9
6
3
50 100 150 200 250 300 350 400
入射面分辨力,mm
GJB 1580A-2004
9
两点间距离。沿与隔声层取向垂直的方向移动探头进行扫查时,扫查间距应不大于两者中较小的有效声
束宽度的二分之一。
4.2.5 质量验收
4.2.5.1 质量验收等级的规定见表 4。图样中应指定所要求的等级。当一个零件需用多个等级时,在
图样上应划出区域并指定所要求的等级。在本标准中未包括的任何其它质量要求应由供需双方另行商
定。
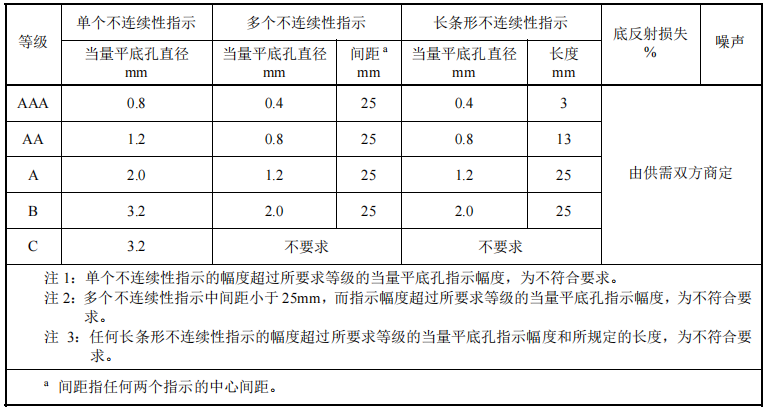
4.2.5.2 检验人员认为影响使用的异常情况应详细记录,并提交有关部门分析处理。
4.2.5.3 在所用探头近场距离为 N 的情况下,若平底孔孔底位于大于 3N 的距离时,且所有信号幅度
值均处于检验仪的垂直线性范围内,则不同直径平底孔的反射波高之间的关系见图 5。
4.2.6 不连续性的评定
4.2.6.1 平面位置的确定
4.2.6.1.1 对于接触法,处于探头远场区的不连续性,只需将探头在受检件表面移动,即可获得不连
续性的最大反射波高所在位置,也就是不连续性的平面位置。对处于探头近场区的不连续性,则应考虑
声束横截面内声压的峰值分布。
4.2.6.1.2 对于液浸法,在探头主声束垂直于受检件表面移动,获得不连续性的最大反射波高后,将
一吸声材料的薄片斜靠声入射面移动,当移动到反射波高下降 6dB 的位置,沿着此薄片的边,在入射
面上画一直线,在其它两个方向上重复同样的操作,三条线将在声束入射点处相交,此交点即为不连续
性的平面位置。
4.2.6.2 埋藏深度的确定
用声性能与受检件相同(或声速已知)且厚度已知的材料对检测仪显示屏时基线进行校准后,不连续
性的埋藏深度可从时基线上反射信号的位置直接读出。也可将上表面反射波与不连续性反射波之间的间
距与上、下表面反射波之间的间距相比较,计算出不连续性深度与受检件厚度之比,在测量出受检件厚
度后,计算出不连续性的埋藏深度。
对于液浸法,当探头声束不垂直于入射面时,在按 4.2.6.1.2 确定声束入射点后,根据探头声束入射
角,求出声束在受检件中折射角,亦可计算出不连续性的埋藏深度。
4.2.6.3 当量尺寸的评定
GJB 1580A-2004
10
a
相邻孔径的分贝差。
图 5 幅度与平底孔大小间的关系
4.2.6.3.1 若不连续性的埋深与平底孔的埋深相同,可将不连续性反射波高与平底孔的反射波高直接
比较。此时,若不连续性反射波高与平底孔的反射波高相同,则该平底孔的尺寸即为不连续性的当量尺
寸。若不连续性反射波高与平底孔的反射波高不相同,应用衰减器记录下两者的分贝差。在进行比较时,
仪器的调整、用液浸法时液程的深度均应相同。且一般波高应调整到显示屏满刻度的 50%~80%之间。
4.2.6.3.2 若不连续性的埋深与所有试块中的平底孔的埋深均不同,则可用两个埋深与之相近的试块,
用插入法进行评定,不允许使用外推法。
4.2.6.3.3 必要时,可利用能使不连续性位于远场区的探头。
4.2.6.3.4 在声束垂直入射到受检件表面时,由于可能存在不连续性的不同取向,使所获得的不连续
性反射波高可能并不是可获得的最大反射波高。对于液浸法,可从不同角度对不连续性进行评定;对于
接触法,可通过对背反射损失的监测来判断。
4.2.6.3.5 在可能的情况下,还应从背面对不连续性进行评定。因为不连续性的反射能力随声束入射
方向的不同可存在很大差异。
4.2.6.4 不连续性长度的评定
对于长条形不连续性,在有必要对其长度作出评定时,可按下述方法进行:
a) 探头在试块上移动,使来自平底孔孔底的反射波高达到最大,平底孔与不连续性的埋深相同,
平底孔的直径应符合表 4 中关于长条形不连续性当量平底孔直径的规定,调节仪器的衰减器,
使平底孔的反射波高为显示屏满刻度的 80%,沿平底孔径向移动探头直至反射波高降至显示
屏满刻度的 10%;然后反方向移动探头,经过 80%的波高点直至再次降至 10%。记下两个 10%
之间的距离 L1;
b) 在仪器调整不变的情况下,将探头移放在长条形不连续性一端的反射波高为满刻度 10%的点
上,然后将探头移放在长条形不连续性另一端的反射波高为满刻度 10%的点上,记下两点之
间的距离 L2;
c) 不连续性的长度按(L2-L1)评定。
4.2.6.5 底反射损失的评估
4.2.6.5.1 在扫查过程中,对噪声幅度高于正常噪声一倍处或底反射波高明显下降处,以及重要零件
在形状允许的任何部位,均应进行底反射损失的评估。
4.2.6.5.2 评估的方法为:在正常组织的相同或相似零件的相应部位上,用衰减器将底反射信号幅度
降至显示屏满刻度的 80%,然后将探头放在受检件上以确定背反射的损失。应观察入射点和背面情况,
平底孔直径,mm
dBa
直径,mm 面积,mm2 相对幅度
(线性放大器) 平底孔面积比 2︰1,幅度相差 6dB
平底孔直径比2︰1,幅度相差12dB 20
15
10
50 -5 -10
-15
-20
0.5 1.0 1.5 2.0 2.5 3.0
0.8
1.2
1.6
2.0
2.4
2.8
3.2
3.2
2.8
2.4
2.0
1.6
1.2
0.8
0.4
8
6.2
4.5
3.1
2.0
1.1
0.5
0.12
233457
12
400%
200%
100%
50%
25%
12.5%
200%
100%
50%
25%
12.5%
12.5%
25%
50%
100%
相对回波幅度,dB
GJB 1580A-2004
11
以确定底反射损失不是由表面状态或上下面的不平行引起的。
5 横波检验
5.1 适用性
横波检验主要用于受环向应力、扭曲载荷或弯曲载荷的关键零件和相应的原材料,以及不连续性的
取向与入射面成较大夹角时。
5.2 检验
5.2.1 平表面受检件
除非另有规定,用横波扫查截面厚度不小于 25mm 的平表面零件或异形零件的平面部位时,采用
45˚±2˚的折射角,而当截面厚度小于 25mm 时,采用 60˚±2˚的折射角。
5.2.2 实心圆柱体受检件
5.2.2.1 圆柱体锻件或轧制件应采用纵波检验,必要时再增加横波检验。
5.2.2.2 对于直径 20mm 以上的实心圆柱体的纵波检验,可采用附录 D 中的柱面对比试块进行灵敏度
调整,垂直纵轴进行扫查,用以探出圆柱体中心或靠近中心处的不连续性。横波检验可使用附录 F 所
示试块,如图 6、图 7 所示,用指定的横孔调整灵敏度。
d—探头偏置距离;r—圆柱体半径
图 6 圆柱体的斜入射周向检验示意图
α—边缘声束在柱面的入射角
图 7 用接触法横波对圆柱体进行周向检验示意图
探头
入射声束
折射声束
d r
有机玻璃斜楔
棒
探头
换能器 α
GJB 1580A-2004
12
5.2.2.3 对用于重要零件(如高速旋转件)、直径为 16mm~40mm 的实心圆柱体(含棒材),可用图 8
所示方法进行纵波检查,用附录 D 所示试块进行灵敏度调整,但尺寸 B1 部分可不用。再按图 7 所示的
方法,进行周向斜入射横波扫查,每一受检件需进行顺时针和逆时针或将纵轴作 180˚转向后的横波检
查。以附录 F 所示试块中的横孔进行灵敏度调整。也可用液浸法进行检验。
5.2.2.4 在所有情况下,均应对整个圆柱面进行扫查,扫查间距应不超过声束有效宽度的二分之一。
当出现稳定的反射信号,并判定不是由表面状态引起的,均应作出标记。
图 8 用双探头对圆柱体进行径向检验示意图
5.2.3 圆筒形受检件纵向不连续性
5.2.3.1 用液浸法检验时,应使纵波声束从外圆周入射,可采用倾斜或偏置探头的方法,获得所需的
折射角。图 9 给出了折射横波的中心声束与受检件内壁相切时的情况。
调整的步骤为:将附录 G 中所示的试块放在转动夹具上,使其能绕纵轴作平稳的旋转。调节探头
位置,使探头位于垂直于受检件的纵轴,操纵探头使受检件表面反射波幅度最大,并保证在扫查区内受
检件两端的液程相同。按图 9 所示,倾斜或偏置探头,直至规定的人工反射体的反射波高最大。调节检
测仪的增益,使该反射波的幅度为显示屏满刻度的 80%。 φ,θ—中心声束的入射角和折射角;VLM—水中纵波速度;VSM—圆筒壁中横波速度;
d—探头中心声束轴的偏置距离;R—圆筒形受检件外径;r—圆筒形受检件内径
图 9 检验圆筒形受检件时探头调节示意图
有机玻璃斜楔
发射
棒
接收
φ VLM
θ d θφ
探头
水
聚焦纵声束
φ R R
r
r θ φ sin sin
SW
M V = VL R V d V (sin )
SW
= LM θ
GJB 1580A-2004
13
5.2.3.2 对于给定的直径和壁厚,探头调整完毕后,每一受检件都应进行顺时针方向的横波检验和逆
时针方向或将纵轴作 180˚转向后的横波检验。扫查间距应不超过有效声束宽度的二分之一。当出现稳
定的反射信号,并判定不是由表面状态引起的,均应作出标记。
5.3 评定
对于斜入射的检验,一般情况下,由于不能确定不连续性反射面的方位,不宜仅根据反射波的幅度
就对反射体尺寸作出评估。必要时,应从不同方向入射以获得更多信息,再作评定。
GJB 1580A-2004
14
附 录 A (规范性附录)
超声检验仪与探头配用时的使用性能测试方法
A.1 垂直极限和垂直线性的测定
将纵波直探头耦合在图 A.1 所示试块的检测面上,移动探头,使孔 A 的反射波高 HA与孔 B 的反射
波高 HB之比为显示屏满刻度的 60%∶30%(设 HA>HB)。调节仪器的增益控制旋钮,使 HA以显示屏满
刻度的 10%或更小的增、减量变化。记录 HA及相应 HB的波高,并用图 A.2 所示图形表示。
垂直极限指的是当增益增大时,反射波高 HA在显示屏上所能获得的最大高度。
垂直线性范围由超过或低于调定点而最先与极限线相交的点来确定。线性上限由相应的 HA给出,
线性下限由相应的 HB给出。
单位为毫米
20 1
25 1
50 1 25 1
20 0.5
Φ1.2 0.1
检测面
AB
注 1:试块材料为铝或钢。
注 2:堵孔材料为不溶于水的塑料。
图 A.1 测量垂直线性用试块形状和尺寸
A.2 水平极限和水平线性的测定
将纵波直探头耦合到厚度适当、上下表面平行的试块上。调节仪器的增益、扫描延迟和扫描长度控
制旋钮,以显示出 11 次无干扰的底面反射波;然后调节扫描控制旋钮,使第三次和第九次底面反射波
的前沿分别准确地调定于显示屏水平标尺满刻度的 20%和 80%处。读出并记录其余各多次底面反射波
的位置。在测量每一底面反射波的位置之前,应将其幅度调到显示屏满刻度的 50%。若第 11 次底面反
射波有干扰,可以利用六次底面反射波,此时,可将第二次和第五次底面反射波的前沿调定在水平标尺
满刻度的 20%和 80%处。
水平极限指的是在显示屏水平标尺范围内,可以显示的最大扫描轨迹长度。
水平线性范围可用完全落在所规定允许偏差范围(允许偏差不大于满刻度的 3%)内的一组相邻接点
的位置来给定。参见图 A.3。 75 1
25 1 32 1
GJB 1580A-2004
15
图 A.2 用于确定垂直线性范围的图形
图 A.3 用于确定水平特性的图形
A.3 灵敏度和信噪比的测定
将纵波直探头耦合到铝合金试块上,该试块中含有埋深不小于 75mm、直径为 0.4mm 的平底孔。
调节增益,使平底孔反射波高达到满刻度的 100%,以此评价灵敏度水平,并测量此时的噪声水平,评
价信噪比。
HB,%
线性极限线
理想线性线
调定点(80,9)
例:读出点(53,6)
偏差为满刻度的 3%
理想线性线
调定点(20,3)
在荧光屏水平标尺上信号的位置,
100
90
80
70
60
50
40
30
20
10
0 10 20 30 40 50 60
(44,100) (56,100)
(29,60)
(31,60)
(0,0)
(6,0)
11
10
987654321 0 10 20 30 40 50 60 70 80 90 100
H ,% A
底反射次数
GJB 1580A-2004
16
若孔底反射波高达到满刻度的 100%时,噪声水平低于 20%,则可提高增益,记录不使噪声电平超
过满刻度 20%所保留的可用增益(即灵敏度余量,以分贝计)。 A.4 入射面分辨力和底面分辨力的测定
在仪器校验时,入射面分辨力的测定可采用直径 1.2mm 平底孔的铝合金标准试块。采用换能器直
径不大于 14mm 的 5MHz 纵波直探头,在孔底反射波高为满刻度 80%,而与相邻界面反射波的相交处
不大于满刻度 20%的条件下,测定可分辨的平底孔埋深。参见图 A.4a)。
在需要时,可用图 A.4b)所示试块,测定入射面和底面分辨力,试块的材质、平底孔的直径及孔底
到相邻界面的距离应根据受检件的要求确定。测定时应采用实际检验所需探头,在根据需要所确定的灵
敏度下,找出平底孔反射波与相邻界面反射波的相交处不大于满刻度 20%时,可分辨的平底孔埋深。
此时,入射面与底面分辨力可用从孔底到相邻界面的最短金属距离、孔径及灵敏度大小来给出。
时基线
入射面分辨力
入射面指示
满刻度
噪声信号最大为满刻度的20%
底面分辨力
参考电平指示
孔的指示最小为满刻度的80%
底面信号
100
80
60
40
20
a) 典型图形
试块厚度 h、孔径及表面粗糙度由检验要求确定;孔之间、孔与侧壁之间的距离不应小至引起干涉;孔用塞封堵。
b) 试块示意图
图 A.4 用于确定入射面及底面分辨力的试块及典型图形
A.5 衰减器的校验
A.5.1 将频率为5MHz的纵波直探头耦合到平底孔直径为2mm、孔底至入射面的金属距离大于探头近
场长度的铝或钢试块上,并使孔底的反射波高为最大。在所有的衰减器转接开关均处于断开的情况下,
调节接收器增益控制旋钮,使孔底反射波高为满刻度的100%,固定探头位置及增益旋钮的位置。
A.5.2 用衰减器转接开关,从 1dB 到 21dB,每次增加 1dB(或 2dB,由衰减器的最小步进量决定)的
衰减量,并在“分贝衰减器校验数据记录表”(见图 A.5)的相应位置上,记下每一步所得的孔底反射波
高作为“A”值。
A.5.3 将衰减器转接开关调到接入 10dB 的衰减量,重新调节接收器增益控制旋钮,使孔底反射波高
为满刻度的 100%(必要时可改用较大反射面)。利用衰减器转接开关,从 10dB 到 31dB,每次增加 1dB(或
2dB)的衰减量,并在“分贝衰减器校验数据记录表”(见图 A.5)的相应位置上,记下每一步所得的孔底
支撑 底面分辨力
入射面分辨力
h
GJB 1580A-2004
17
反射波高作为“B”值。
A.5.4 将衰减器转接开关调节到接入 20dB 的衰减量,将孔底反射波高调节到满刻度的 100%。记下从
20dB 到 41dB,每次增加 1dB(或 2dB)的衰减量时孔底反射波高作为“C”值填入图 A.5 中。
A.5.5 继续进行衰减器的校验直至衰减量最大。
A.5.6 每一步的数据均落在表 A.1 中所注明的范围内,为符合要求。
表 A.1 分贝衰减器校验数据表
显示屏满刻度百分数
极限
衰减量
dB 标准值
最小 最大
0 100.0 − −
1 89.1 85 94
2 79.4 75 84
3 70.8 66 75
4 63.1 59 68
5 56.2 52 61
6 50.1 46 55
7 44.7 40 49
8 39.8 35 44
9 35.5 31 40
10 31.6 27 36
11 28.2 24 33
12 25.1 21 30
13 22.4 18 27
14 20.0 15 25
15 17.8 13 22
16 15.8 11 20
17 14.1 10 19
18 12.6 8 17
19 11.2 7 16
20 10.0 5 15
21 8.9 4 13
GJB 1580A-2004
18
显示屏满刻度百分数
极限 记录值 衰减量
dB 标准值
最小 最大 A B C …
0 100.0 − −
1 89.1 85 94
2 79.4 75 84
3 70.8 66 75
4 63.1 59 68
5 56.2 52 61
6 50.1 46 55
7 44.7 40 49
8 39.8 35 44
9 35.5 31 40
10 31.6 27 36
11 28.2 24 33
12 25.1 21 30
13 22.4 18 27
14 20.0 15 25
15 17.8 13 22
16 15.8 11 20
17 14.1 10 19
18 12.6 8 17
19 11.2 7 16
20 10.0 5 15
21 8.9 4 13
图 A.5 分贝衰减器校验数据记录表
GJB 1580A-2004
19
附 录 B (资料性附录)
人工反射体的硅橡胶覆型检查方法
人工反射体的硅橡胶覆型检查方法如下:
a) 用医用注射器抽取丙酮,冲洗干净人工反射体的内腔,并用热风干燥;
b) 用脱模剂微湿润的棉球,仔细轻擦内腔;
c) 按照一定比例,将硫化剂加入所需数量的硅橡胶中,并搅拌均匀;
d) 将配好的胶液缓缓注入人工反射体的内腔。为便于取出覆型物,在灌胶后应插入一段刚性细金
属丝;
e) 将灌好胶的试块立即移入真空箱中抽真空,抽真空开始后,视胶液排气情况反复破真空、抽真
空 2~3 次,胶液中气泡排净后,可将试块取出,放置于室温空气中固化;
f) 等胶液完全固化后,小心取出覆型物,在显微镜下观测。
GJB 1580A-2004
20
附 录 C (规范性附录)
纵波检验用标准试块
C.1 纵波检验用标准试块形状和尺寸
纵波检验用标准试块的形状和尺寸见图 C.1 和表 C.1。
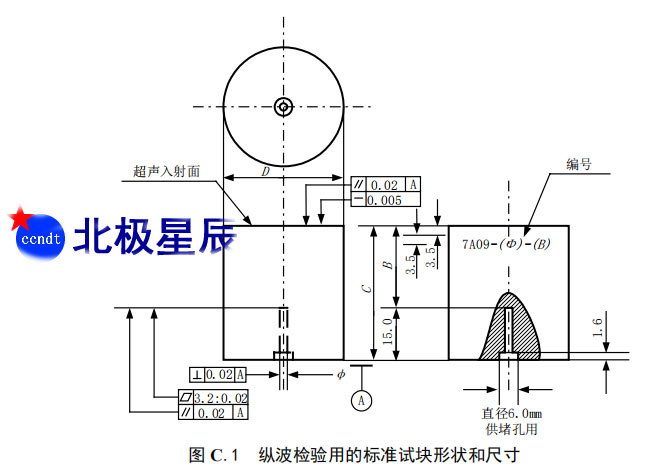
A 图 C.1 纵波检验用的标准试块形状和尺寸
C.2 纵波检验用标准试块的其它要求
纵波检验用标准试块的其它要求如下:
a) 当 B≤150mm 时,试块外径 D≥50mm;当 B>150mm 时,D≥75mm;
b) 编号顺序为:材料牌号(7A09)―平底孔直径(Φ)―埋深(B),如材料牌号为 7A09、平底孔直
径为 1.2mm、埋深为 50mm 的试块编号表示为 7A09-Φ1.2-50;
c) 由加工造成的毛刺均应去除。上下面的外边应磨圆,R 应小于 0.8mm;
d) 材料的牌号为 7A09,热处理状态为 T6;
e) 超声波入射面粗糙度 Ra 值应为 1.6µm;
f) 平底孔的中心线与以圆柱体中心线为基准的同轴度公差不大于 0.1mm。平底孔孔底的表面粗糙
度 Ra 值应不大于 3.2µm。 C
15.0 B
3.5
3.5
1.6
GJB 1580A-2004
21
表 C.1 纵波检验用标准试块尺寸
尺寸 平底孔直径Φ
mm
平底孔埋藏深度 B
mm
柱高 C
mm
公差
±0.01 或孔径的 1%,取
其中较大者
±0.1 ±0.2
系列 1 0.8
系列 2 1.2
系列 3 2.0
系列 4 3.2
2.5
5.0
7.5
10
15
20
25
30
35
40
45
50
60
70
80
90
100
110
120
…
17.5
20
22.5
25
30
35
40
45
50
55
60
65
75
85
95
105
115
125
135
…
GJB 1580A-2004
22
附 录 D (规范性附录)
曲面纵波检验用对比试块
D.1 柱面纵波检验用对比试块
D.1.1 柱面纵波检验用对比试块形状和推荐的尺寸见图 D.1 和表 D.1。
71 %
25
25
25 25
25
25 25
15
15
l1 l2 l2
3.2:0.02
R θ θ
θ应为 90˚±0.5˚;R 的公差为±0.5mm。 图 D.1 柱面纵波检验用对比试块
表 D.1 纵波柱面检验试块尺寸 单位为毫米
R B1 B2 B3 D l1 l2
100 50 100 150 12 40 40
90 45 90 135 12 40 40
75 38 75 113 12 25 40
60 30 60 90 12 25 40
50 25 50 75 12 25 40
40 20 40 60 12 25 40
32 16 32 48 12 25 40
25 12 25 38 10 25 40
20 10 20 30 8 25 25
12 6 12 18 5 25 25
D.1.2 柱面纵波检验用对比试块的其它要求如下:
a) B1、B2、B3 分别为圆柱体直径的 1/4、1/2 和 3/4,公差为 0.2mm。
b) 根据检验要求,平底孔直径可选为 0.8mm、1.2mm、2.0mm 和 3.2mm。
c) 上下面平行度应在±0.025mm 以内。
单位为毫米
B3 B2 B1
GJB 1580A-2004
23
d) 平底孔直径公差为±0.01mm 或孔径的±1%,取其中较大者;孔底平面度应为 0.01mm;孔底表
面粗糙度 Ra 值应不大于 3.2µm;各孔的中心线应通过半径,同轴度公差为 0.1mm。
e) 平底孔应经防腐蚀处理并应密封,以提供金属-空气界面。
f) 可将图 D.1 中的试块做成分开的三块,一块为 B1 尺寸,一块为 B2 尺寸,一块为 B3 尺寸。对于
B1 尺寸试块,15mm 改为 25mm。对于 B2 尺寸试块,尺寸 l2及所注的 15mm 均改为 25mm。对
于 B3 尺寸试块,尺寸 l2 改为 l1 尺寸。其它要求不变;
g) 试块曲率半径应与受检件相同或接近。
D.2 圆筒形制件纵波检验用对比试块
D.2.1 圆筒形制件纵波检验用对比试块示意图见图 D.2。
50 %
平底孔
θ
θ应为 90˚±0.5˚。 图 D.2 圆筒形制件纵波检验用对比试块示意图
D.2.2 圆筒形制件纵波检验用对比试块的其它要求如下:
a) 根据检验要求,平底孔直径可选为0.8mm、1.2mm、2.0mm和3.2mm。平底孔直径公差为±0.01mm
或孔径的±1%,取其中较大者;孔底平面度应为0.01mm;孔底表面粗糙度Ra应不大于3.2µm;
各孔的中心线应通过半径,同轴度公差为0.1mm。平底孔应经防腐蚀处理并应密封,以提供金
属-空气界面。
b) 试块曲率半径应与受检件相同或接近。
GJB 1580A-2004
24
附 录 E (规范性附录)
横波检验用平表面试块
E.1 横波检验用的平表面试块 A E.1.1 横波检验用的平表面试块 A 的形状和尺寸见图 E.1。
单位为毫米
φ3.2φ2.0φ1.2φ0.8
附加横孔
C面 θ
3.2:0.03
T tanθ2T tanθ L φ2.0通孔
A面 αθ
25.4:0.03 B B面
(3/4)T.tanθ+12.7
B φ2.0通孔
α—声束入射角
φ2.0通孔
θ . . 图 E.1 横波检验用平表面试块 A 形状和尺寸
E.1.2 平表面试块 A 厚度、长度与受检件材料厚度的对应关系见表 E.1。 表 E.1 平表面试块 A 厚度、长度与受检件材料厚度的对应关系
受检件材料厚度 h
mm
试块厚度 T
mm
试块长度 L
mm
≤25 20 或 h >25~50 40 或 h >50~100 80 或 h >100~150 130 或 h >150 h+25
3T·tgθ+25
26 T/(2cosθ)
20.0 20.0 20.0 20.0 20.0
25.0
25.0
T/4
T T/4
T/2
D
GJB 1580A-2004
25
E.1.3 平表面试块 A 的其它技术要求如下:
a) 根据采用的验收等级,选用相应的的孔径。
b) 试块上可包括所有等级的平底孔,若试块只用于较少等级时,可使用有较少孔的窄试块。平底
孔孔底的平面度应为 0.01mm,孔底表面粗糙度 Ra 值应不大于 3.2µm。
c) 横孔表面粗糙度 Ra 值应不大于 1.6µm。
d) 当只使用 1/2~1 个跨距检验较厚的材料时,可使用比图示较短的试块,短试块上的横孔应沿 L
重新定位,使各孔的位置与探测其它孔时的所有声通道至少相距 20mm。
e) θ为试块中的折射角。一般情况下,当 T 在 12.5mm~25.4mm 范围内时,θ为 60˚;当 T 大于
25.4mm 时,θ为 45˚。
f) A、B、C 三面的表面粗糙度应与受检件相同。
g) 除孔直径公差为规定值的±3%外,所有其它尺寸的公差均为±0.8mm。
h) 厚度大于25mm的试块,可从C面增加一些Φ2.0mm的横孔,使各横孔轴线距A面分别为7mm、
13mm、25mm、38mm 和 50mm 等。直至距 B 面 T/4 为止。各孔沿 L 的位置分布无特殊要求,
但各孔与探测其它孔时的所有声通道至少相距 20mm。
i) 所有孔应永久性封堵,以防止进水和保持空气―金属界面。
E.2 横波检验用的平表面试块 B E.2.1 横波检验用的平表面试块 B 的形状和尺寸见图 E.2。
单位为毫米
25 K A 0.05
L
0.13
0.05
AA φ 图 E.2 横波检验用平表面试块 B 形状和尺寸
E.2.2 平表面试块 B 的其它技术要求如下:
a) 图 E.2 中孔全部为横孔,孔表面粗糙度 Ra 值应不大于 1.6µm;孔直径公差为规定值的±3%;
可根据使用要求,增减孔的数量;推荐孔径Ф不大于 1.0mm,孔长度 lk 为 12mm。
b) 孔间距 K 不小于 20mm,若探头折射角为θ,探头尺寸为 l,孔与入射面距离为 H,则 H 最大
的孔与侧边的距离不应小于 L,L 按公式(1)计算:
L=H•tgθ+l …………………………………………(1)
c) 试块表面粗糙度应与受检件相同。
d) 所有孔应封堵,以防止进水和保持空气―金属界面。
36
10
13
16
19
22
25
32
H A 0.05
25
Lk
GJB 1580A-2004
26
附 录 F (规范性附录)
实心圆柱体对比试块
F.1 直径大于 50mm 实心圆柱体对比试块
F.1.1 直径大于 50mm 实心圆柱体周向检查用对比试块形状和尺寸见图 F.1。 3D/8 D/4
D/16
d1 d2 ABC EFG
90 1
6处 图 F.1 直径大于 50mm 实心圆柱体周向检查用对比试块形状和尺寸
F.1.2 直径大于 50mm 实心圆柱体对比试块其它要求如下:
a) 横孔 A、B、C 直径为 0.5mm±0.03mm,深度 d1 为 13mm±0.5mm。
b) 横孔 E、F、G 直径为 1.2mm±0.03mm,深度 d2 为 25mm±0.5mm。
c) 横孔位置公差为±0.25mm。
d) 所有孔表面粗糙度 Ra 值应不大于 1.6µm。
e) 试块表面粗糙度应与受检件相同。
f) 所有孔应永久性封堵,以防止进水和保持空气―金属界面。
F.2 直径不大于 50mm 实心圆柱体对比试块
F.2.1 直径不大于 50mm 实心圆柱体周向检查用对比试块形状和尺寸见图 F.2。
10
10
60
φ0.8 0.02
φ0.8 0.02
图 F.2 直径不大于 50mm 实心圆柱体周向检查用对比试块形状和尺寸
F.2.2 直径不大于 50mm 实心圆柱体对比试块其它要求如下:
a) 横孔位置公差为±0.25mm。
b) 所有孔表面粗糙度 Ra 值应不大于 1.6µm。
c) 试块表面粗糙度应与受检件相同。
d) 所有孔应永久性封堵,以防止进水和保持空气―金属界面。
单位为毫米
d2F ≥60
D/8
D/4 7D/16
D D 1.5 D/5
GJB 1580A-2004
27
附 录 G (规范性附录)
圆筒形对比试块
G.1 壁厚为 3mm~25mm 的圆筒形试块的示意图见图 G.1。平底孔直径Φ可为 0.8mm、1.2mm、2.0mm
和 3.2mm。平底孔直径公差为±0.01mm 或孔径的±1%,取其中较大者;孔底平面度应为 0.01mm;孔
底表面粗糙度 Ra 值应不大于 3.2µm;孔轴线应通过管壁中心,偏差应不大于管壁厚度的±2%;孔轴线
应与半径垂直,偏差应在±2˚以内;孔底面应在半径上。平底孔应经防腐蚀处理并应密封,以提供金属
-空气界面。试块曲率半径应与受检件相同或接近。
单位为毫米
Φ R R—管壁中心圆半径
图 G.1 壁厚为 3mm~25mm 的圆筒形试块的示意图
G.2 壁厚不大于 3mm 的圆筒形试块的示意图见图 G.2。A 面应在半径上。
A-A
A面 AA 图 G.2 壁厚不大于 3mm 的圆筒形试块的示意图 10 2
中 华 人 民 共 和 国
国家军用标准
变形金属超声检验方法
GJB 1580A-2004
*
国防科工委军标出版发行部出版
(北京东外京顺路 7 号)
国防科工委军标出版发行部印刷车间印刷
国防科工委军标出版发行部发行
版权专有 不得翻印
*
开本 880×1230 1/16 印张 2 14 字数 65 千字
2004 年 11 月第 1 版 2004 年 11 月第 1 次印刷
印数 1-400
*
军标出字第 5623 号 定价 18.00 元
GJB 1580A-2004