一.探伤检测前的准备 1. 数字超声波探伤仪主机 2. 横波斜探头:2.5M13×13K2 3. 标准试块:CSK-IA 、CSK-IIIA 4. 30mm厚钢板的对接焊缝 5.DAC参数: (1)DAC点数:d=5、10、15、20(mm)的4点 (2)判废线偏移量:-4dB (3)定量线偏移量:-10dB (4)评定线偏移量:-16dB 6.耦合剂(如:机油等) |
|
二.探测面的选择
焊缝一侧
三.开机
1.将探头和超声探伤仪主机连接
2.开启面板开关,开机自检,进入探伤界面。
四.校准
1.输入材料声速:3230m/s
2. 探头前沿校准
(1)如图1所示,将探头放在CSK-IA标准试块的0位上
(2)前后移动探头,使试块R100圆弧面的回波幅度最高,回波幅度不要超出屏幕,否则需要减小增益。
(3)当回波幅度达到最高时,保持探头不动,在与试块“0”刻度对应的探头侧面作好标记,这点就是波束的入射点
(4)前沿距离校准:
从探头刻度尺上直接读出试块“0”刻度所对应的刻度值,即为探头的前沿值。(或用刻度尺测量图1所示L值,前沿x=100-L。)
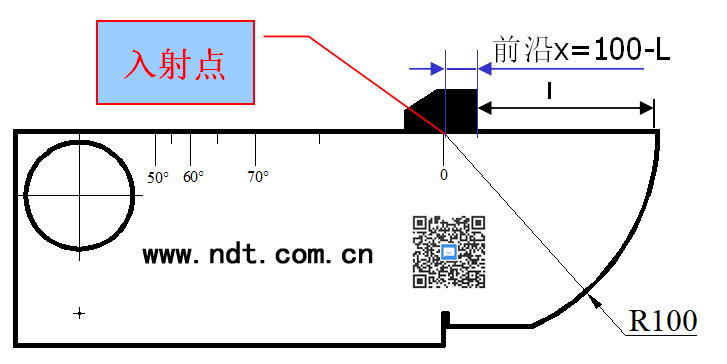
(图1)CSK-IA试块校测零点和前沿示意图
3.探头零点的校准
按图1的方法放置探头,用闸门套住最高波,调整探头零点直到声程S=100
4.探头K值校准(折射角的校准)
由于被测物的材质和楔块的磨损会使探头的实际K值与标称值有一些误差。因此需要测定探头的实际K值。校准步骤如下:
(1)如图2将探头放在CSK-IA标准试块的适当的角度标记上。
(2)前后移动探头,找到试块边上大圆孔的回波波峰时,保持探头不动。
(3)在试块上读出入射点与试块上对齐的K值,这个角度为探头的实际K值,将此值输入。(或者通过计算斜率校准,见下图2)
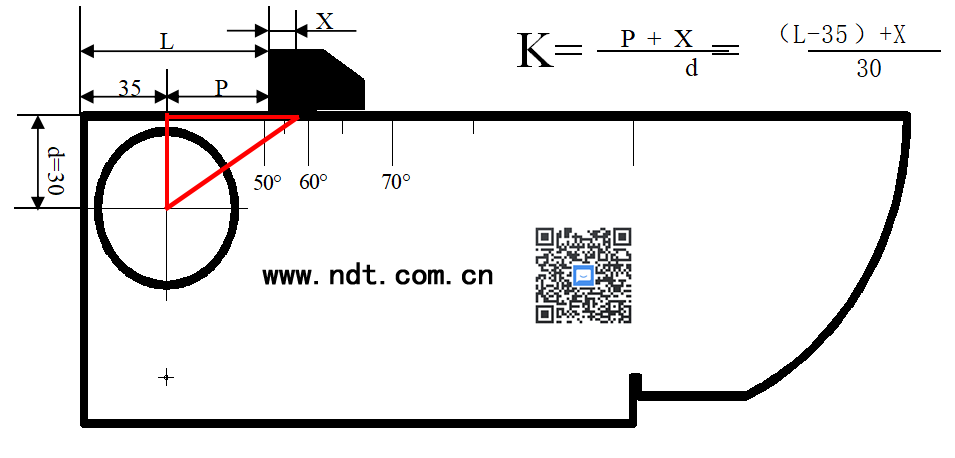
(图2:折射角的校准)
五.DAC曲线的制作及标准的输入
1.制作DAC曲线
①:按【DAC】键,启动DAC菜单。
②:如下图所示,将探头放在CSK-IIIA试块①的位置,左右移动探头找到深为10mm孔的最高
回波,此波不能超过满屏高度,用A闸门套住此波,按【F3】键,使标定点增加为“1”
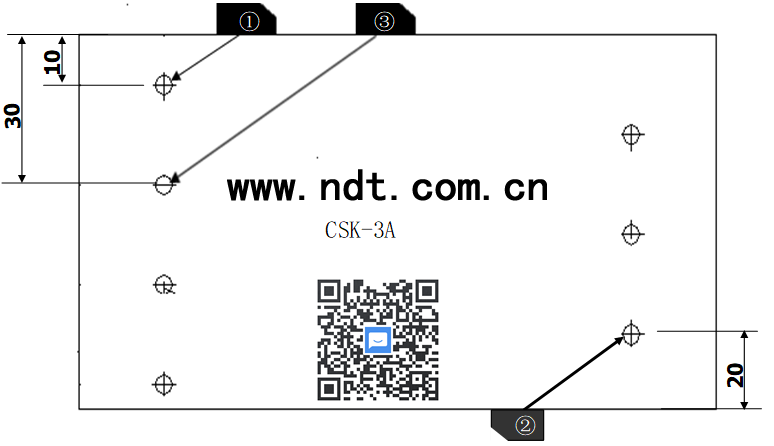
(DAC曲线制作)
③:如图3所示, 将探头放在CSK-IIIA试块②的位置,左右移动探头找到深为20mm孔的最高
回波,此波不能超过满屏高度,用A闸门套住此波,按【F3】键,使标定点增加为“2”;
●此时已添加了2个标定点,DAC开关已自动打开,DAC曲线自动绘制在屏幕上
●重复③的步骤,可以找到孔深为30、40、50mm等反射体的最高回波,使标定点增加为3、4、5...
●标定点可按孔深的任意顺序进行记录
2.DAC偏置设置(探伤标准的输入):
按【F5】键,进入第三页,找到判废线、定量线、评定线设置项
按【F2】键,选择评定线 ,旋转旋钮调节评定线的值,比如设为 -16db
按【F3】键,选择定量线 ,旋转旋钮调节定量线的值,比如设为 -10db
按【F4】键,选择判废线 ,旋转旋钮调节判废线的值,比如设为 -4db
3.设置表面补偿和评估曲线
按【F5】键,进入第四页
按【F2】键选择表面补偿 ,旋转旋钮设定工件表面补偿值,一般设为+4db
按【F5】键选择评估曲线 ,旋转旋钮,一般设定为评定线
4.保存通道
按【通道】键,旋转旋钮选择一个空的通道号,按【F3】保存通道
此时,校准的参数和DAC曲线均保存在了通道里。
六.现场探伤
1.通过调整探伤灵敏度,使DAC曲线完整显示在屏幕上,然后开始探伤。
2.探伤时一般是使探头垂直焊口走向并沿焊口走向做锯齿型扫查(即探头运动轨迹为探头);
3.探头沿焊口走向(前后)移动的距离:0~100mm (如:下图)
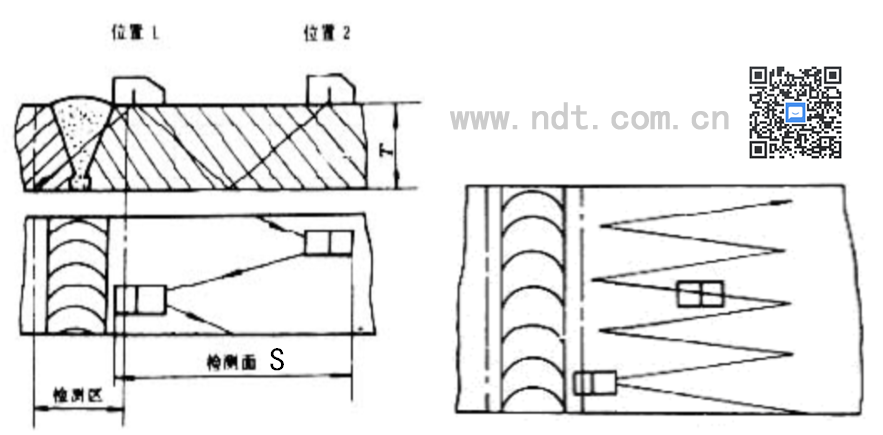
计算方法:起点(位置2):0
终点(位置2):S=2KT=2×2×25=100mm (其中K表示探头斜率,T表示工件厚度)
4. 探头沿焊口走向( 左右)移动的速度:≤1.5 米/分
七.存储探伤波形和数据
将探伤波形和数据存储到相应组号。
八.生成探伤报告
将探伤仪主机与计算机连接,将探伤波形和数据上传到计算机,生成探伤报告。